Summary
Choosing the right linear rails can significantly impact your project`s success. This article delves into essential factors to consider, helping you make informed decisions while highlighting cutting-edge innovations in the field. Key Points:
- Explore advanced materials like high-performance polymers and carbon fiber for enhanced stiffness-to-weight ratios and reduced friction in linear rails.
- Utilize AI-driven predictive maintenance with real-time data to prevent failures, minimize downtime, and improve operational efficiency.
- Consider hybrid linear rail systems that combine various technologies for superior load handling, speed, and precision.
What Are Linear Rails and Why Are They Crucial for Your Project?
A Small Business’s Struggle: Choosing the Wrong Linear Rails
Factor | Description | Importance |
---|---|---|
Load Capacity | Determine the maximum weight your application will carry. | Crucial for ensuring stability and performance. |
Material Selection | Choose between aluminum for lightweight needs or steel for durability. | Affects rigidity, corrosion resistance, and overall lifespan. |
Rail Profile | Decide on square vs round profiles based on stability requirements. | Impacts precision under load and alignment ease. |
Bearing System | Select between linear ball bearings for low friction or roller bearings for robustness. | Influences maintenance frequency and efficiency. |
Environmental Conditions | Assess temperature variations and contaminants in the workspace. | Guides choices for seals or coatings to enhance durability. |
From Frustration to Clarity: How They Found the Right Solution
How We Helped Them Navigate the World of Linear Rails
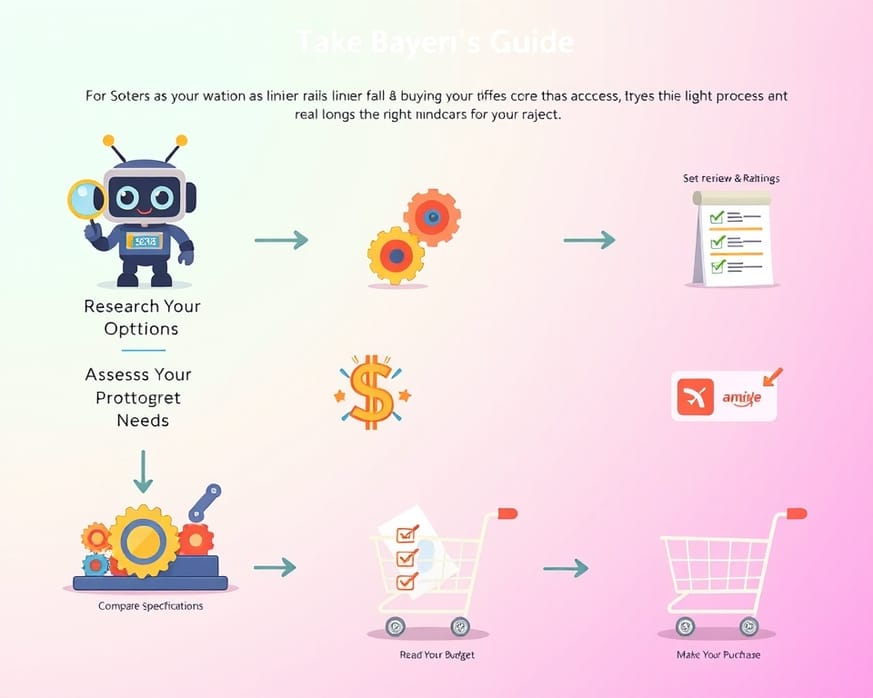
Frequently Asked Questions About Linear Rails
Another popular question revolves around bearing systems. You might wonder which one is best for smooth operation: ball bearings or roller bearings? Well, here's a little insight—ball bearings tend to offer lower friction, which means smoother movement at higher speeds; however, they usually have a reduced load capacity compared to rollers. So if you're looking for speed over sheer strength—or vice versa—you'll want to keep this in mind.
Now let's not forget about rail profiles! Many folks don’t realize that the shape of the rail (square versus round) can significantly affect how easy it is to install and align everything properly. It’s something that can save you time and headaches down the road!
Environmental factors also play a vital role in your selection process. Are temperature variations or contaminants a concern in your workspace? If so, opting for sealed or lubricated systems could provide some much-needed protection.
Lastly, don't underestimate load ratings! It's essential that these match up with both static and dynamic conditions of your project—this ensures longevity and reliability in operation. After all, nobody wants their equipment failing when they need it most!
These considerations may seem like minor details at first glance but trust me—they can make a world of difference in performance and durability as you embark on your project journey! 🌟
What Are the Hidden Factors to Consider When Selecting Linear Rails?
Why Some Engineers Hesitate to Upgrade Their Linear Rails
Step-by-Step Guide to Choosing the Perfect Linear Rails
During my early days in engineering, I faced challenges selecting linear rails for a robotics application. I realized many people overlook critical factors like load capacity and environmental conditions, which ultimately affected performance. That experience taught me the importance of a thorough selection process—one that I’m excited to share with you today!
### Step-by-Step Guide to Choosing the Perfect Linear Rails
**Step 1: Analyze Load Capacity**
Before diving into specifics, determine how much weight your application will carry. If you're working on heavy-duty machinery, opt for hardened steel rails; if precision and lightweight applications are your focus, aluminum may be ideal. (Pro tip: Keep a calculator handy to crunch numbers quickly!)
**Step 2: Consider Rigidity and Accuracy**
Now it's time to think about how precise you need those rails to be. Higher precision usually means investing in ground surfaces and preloaded ball bearings that minimize deflection during operation. This is crucial for projects where accuracy is non-negotiable.
**Step 3: Evaluate Environmental Conditions**
Take stock of where your system will operate. If you're looking at harsh environments or cleanroom setups, stainless steel or specially coated options are essential to prevent corrosion or contamination.
**Step 4: Assess Travel Speed and Lubrication Needs**
Next up is speed! Determine how fast your application needs to move. For high-speed operations, consider self-lubricating rail systems; they reduce maintenance downtime significantly (I personally set reminders every few months just in case!).
**Step 5: Ensure Compatibility with Mounting Configurations**
Finally, check that the linear rails fit seamlessly within your existing setup—this includes mounting configurations and motorized components. A mismatch here can lead to headaches down the line.
### Advanced Tips & Friendly Reminders
If you're looking to delve deeper into advanced applications or want additional insights tailored specifically for niche projects, consider exploring modular rail systems—they offer flexibility as your project's requirements evolve over time.
Remember, taking these steps doesn’t just enhance performance—it also prolongs the life of your equipment! So take a breath; with careful consideration of these parameters, you'll not only select better linear rails but also optimize overall efficiency in ways that might surprise you!
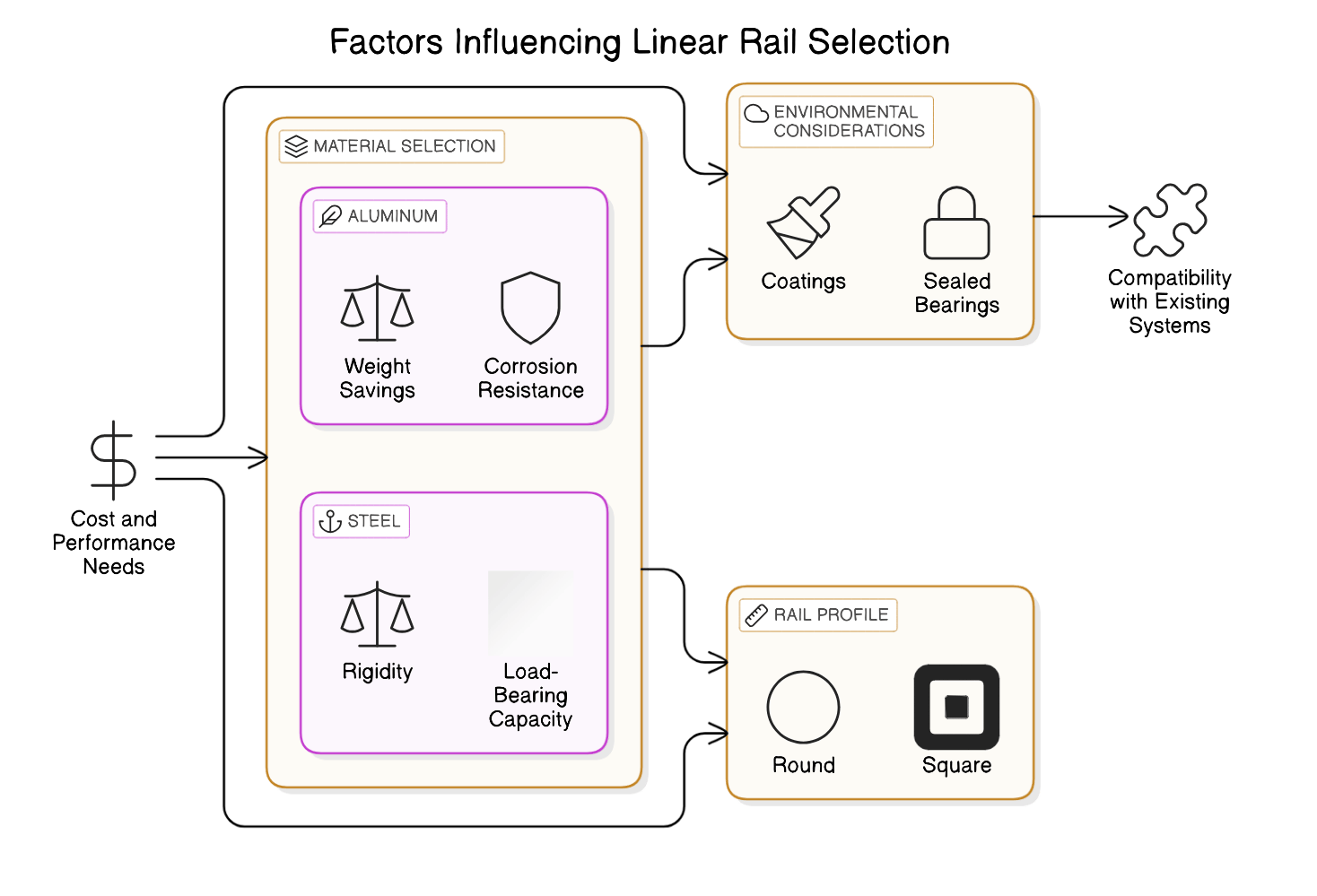
What’s Next in the Evolution of Linear Rail Technology?
Final Thoughts and Actionable Tips for Your Linear Rail Selection
Another crucial aspect is the rail profile itself. You may find that square profiles tend to enhance stability under heavy loads compared to round ones, which can sometimes flex or wobble more easily. This choice could make a substantial difference in how well your system performs over time.
Don’t overlook the bearing system either; choosing between linear ball bearings and recirculating roller bearings can affect maintenance needs as well as overall reliability. While linear ball bearings minimize friction—which is great for efficiency—they may require more frequent upkeep than their roller counterparts, which are generally known for their robustness.
Lastly, precision ratings shouldn't be sidelined in your decision-making process. If your application demands tight tolerances, opting for higher accuracy will be critical in achieving optimal results.
As you assess these factors with respect to your unique application requirements, remember that this isn’t just about making a choice—it’s about positioning yourself effectively within an evolving landscape of motion systems technology. The trends in materials and designs are constantly changing; staying informed helps us adapt rather than get left behind.
So why wait? Take action now and explore how these insights apply to your specific situation—who knows what efficiencies or innovations you might discover!
Reference Source
Essential Guide to Choosing the Right Linear Guide Rail ...
This article delves into the complexities of selecting the right linear guide rail for your projects, highlighting essential considerations ...
Source: 秀觀點Top Five Mistakes in Choosing and Using Linear Guides
The preload of the linear guide needs to be matched to the accuracy that can be achieved with the mounting parts. If it is not possible to meet the accuracy ...
Source: Motion SolutionsEssential Guide to Choosing Stainless Steel Linear Rails ...
This essential guide delves into the latest advancements in stainless steel linear rails, highlighting their significance for various ...
Source: 秀觀點Stay "On-Track" When Selecting a Linear Guide System
One of the essential characteristics to consider is guide rail performance -- primarily based on speed, load-carrying capacity, and moment load limitations.
Books which describe how to properly install ultra precision ...
Basically, the idea is to gradually correct errors by hooking up the plate connecting the linear rail carriages together, but not tighten down ...
Source: Reddit · r/CNCLinear Guide Rails Selection – Where to start?
1.) Check what linear guide rails are used in similar machines · 2.) Assessment of the loads in your case · 3.) Evaluation of the load capacity of ...
Source: the Tuli shopAnd He's Buying a Railway to Heaven: A Linear Guide Rail ...
Aug 25, 2020
Source: Carbide 3D Community SiteTypes of linear guides and mounting options
Basically, miniature rails are more consistent in their with/height (does that even matter) and are available in "precision" grade, while medium ...
Source: RepRap
Related Discussions