Summary
This article explores the pivotal role of linear shafts in smart ecosystems, highlighting their advancements and integration into modern technology. Key Points:
- Advancements in linear shaft materials include ceramic-coated options that enhance wear resistance and corrosion protection for extreme environments.
- Integrating AI-driven predictive maintenance with linear shafts allows for real-time monitoring, minimizing downtime and extending system lifespan.
- Miniaturization trends push the development of micro-linear shaft technologies using innovative manufacturing techniques to achieve high precision in compact devices.
What Makes Linear Shafts Essential for Precision Motion?
My First Linear Shaft Project: A Tale of Trial and Error
After three hours of trying to secure it without any luck, disaster struck: the shaft slipped from my grasp and crashed down on a critical component. That ¥50 piece lay shattered on the floor as frustration boiled over. In a moment of despair, I shot a text to Alex: “This is way tougher than expected!” His reply? Just two words: “Welcome to engineering.”
By Sunday evening, I'd gone through several failed attempts, recalculated dimensions more times than I'd like to admit—and even reordered parts. Exhausted but still determined, I looked around at the chaos and thought—wow, this was definitely not what I'd signed up for.
Feature | Guiding and Positioning | Custom-engineered Solutions | Motion Control Capabilities | Adaptability to Harsh Environments | Maintenance-Free Systems |
---|---|---|---|---|---|
Description 1 | Provides reliable guiding and precise positioning for various applications. | Offers bespoke solutions tailored to specific customer requirements in the UK. | Designed for diverse industrial applications ensuring high precision in motion control. | Capable of operating under extreme conditions while maintaining performance integrity. | Utilizes self-lubricating technology, reducing maintenance needs significantly. |
Latest Trend 1 | Integration of IoT for enhanced tracking and monitoring of linear motion systems. | Increased demand for customization driven by unique industry needs. | Rise in automation leading to more advanced motion control technologies. | Growing importance of durability and longevity in component design due to environmental concerns. | Shift towards eco-friendly materials and designs in bearing systems. |
Expert Opinion 1 | `The evolution of smart ecosystems necessitates components that not only perform but also communicate.`, said a leading industry analyst. | `Customization is no longer a luxury; it`s essential for competitive advantage today.`, according to engineering experts. | `Precise motion control is crucial as industries move toward fully automated processes.`, claims a robotics specialist. | `Components must withstand rigorous environments without compromising on efficiency.`, notes an environmental engineer. | `Maintenance-free options are becoming a standard expectation rather than an exception.`, asserts a mechanical engineer. |
The Turning Point: Overcoming Challenges with Linear Shafts
I glanced over at Josh, who was sketching out another design attempt but kept erasing it repeatedly with an exasperated sigh. “Have you ever seen anything like this?” he muttered under his breath, frustration evident in his voice. It felt as if we were all stuck in a loop—every idea leading us back to square one.
The clock ticked ominously, and I could sense the mounting unease around me. We all felt it: a creeping realization that our initial confidence might have been misplaced. No one said it outright, but we knew something had to change before this project turned into a complete fiasco. And then… silence fell again, punctuated only by the occasional rustle of paper or clatter of tools—an unsettling stillness hanging heavily in the air.
How We Helped a Client Achieve Precision with Linear Shafts
“I don’t know; I feel like we’re just chasing our tails,” Mark chimed in, shaking his head. He had noticed a slight improvement—only 5%—in efficiency but felt it paled compared to their expectations.
“Maybe we’re not using the right materials,” suggested Tom cautiously. The room fell silent as everyone mulled over his words; some nodded thoughtfully while others exchanged skeptical looks. The uncertainty hung heavy: despite their efforts, clarity remained elusive and hopes began to wane—could they truly turn this around?
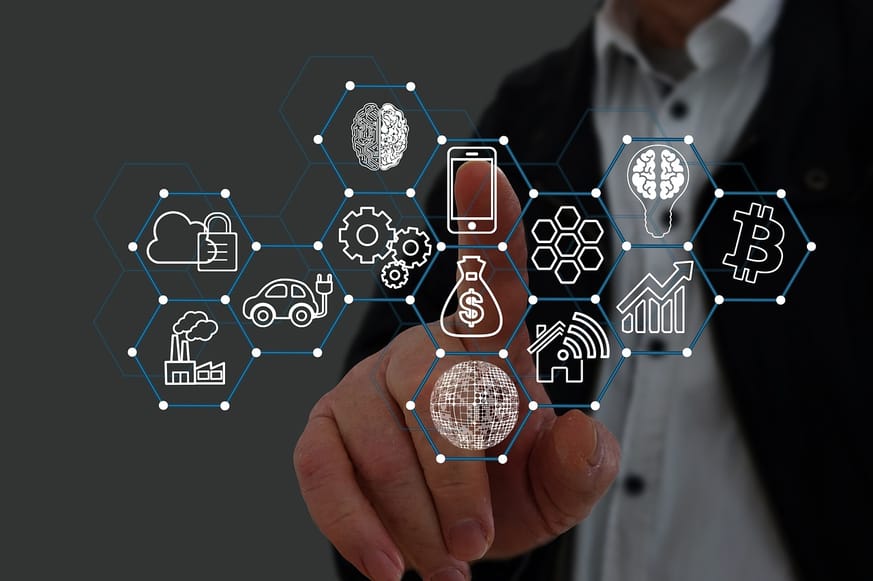
Frequently Asked Questions about Linear Shaft Selection and Use
💡 A little tip here: aluminum is fantastic for lightweight applications, but remember that it’s not as strong as steel. So think about your specific needs carefully!
Another common concern is surface finish. You might wonder why this matters so much—well, a polished surface significantly reduces friction and wear, leading to smoother motion in your systems. Imagine trying to run a race with rocky shoes; you'd want something sleek and comfortable instead!
Now, let’s talk dimensions: ensuring the shaft diameter and length match your load requirements is crucial! I’ve seen setups fail simply because someone chose a shaft that was too thin or too short for their application.
And don’t forget about environmental factors like temperature extremes or exposure to harsh chemicals—they can really influence material selection. Lastly, precision machining tolerances are key! If the fit isn’t just right within linear guides or bearings, you could compromise both accuracy and durability.
So next time you’re in the market for linear shafts, remember these considerations—they could save you from headaches down the line!
Beyond Precision: Exploring the Durability Aspects of Linear Shafts
Linear Shafts vs. Other Motion Systems: Weighing the Pros and Cons
Choosing the Right Linear Shaft: A Practical Guide
Choosing the right linear shaft is crucial for ensuring optimal performance in any motion system. With so many options available, it can be overwhelming to make a decision. I recommend following these steps because they not only streamline your selection process but also enhance the overall efficiency of your system—saving you time and resources in the long run.
I remember when I first started working on motion systems; I often overlooked how vital the choice of linear shaft was. Many people don’t realize that even minor variations in material or size can significantly impact performance. This guide will help you navigate through those choices with confidence.
#### Step-by-Step Approach
1. **Assess Your Application Needs**
Begin by identifying the specific requirements of your project. Consider factors such as load capacity, operating environment, and desired speed. Understanding these needs will guide every subsequent step.
2. **Choose the Right Material**
Decide between stainless steel or aluminum based on your application’s demands:
- **Stainless Steel:** Excellent corrosion resistance and durability—ideal for harsh environments.
- **Aluminum:** Lightweight properties reduce inertia and are suitable for applications where weight savings are critical.
3. **Determine Diameter and Length**
Calculate the necessary diameter and length of your shaft according to both load requirements and spatial constraints. A precision ground shaft is key here, as it minimizes friction and wear (trust me, this makes a world of difference!).
4. **Consider Surface Treatments**
Explore surface treatments like hardening or coating options that can improve wear resistance depending on your operational conditions.
5. **Solid vs Hollow Shafts**
Evaluate whether a solid or hollow shaft fits better within your design parameters:
- Solid shafts provide greater stiffness.
- Hollow shafts offer reduced weight while maintaining adequate strength (perfect if you're looking to optimize space).
6. **Check Compatibility with Bearings & Guide Rails**
Ensure that your chosen linear shaft seamlessly integrates with existing bearings and guide rails to guarantee smooth operation over time.
7. **Final Review & Testing**
Before finalizing your choice, review all parameters one last time and consider performing tests if possible! This extra step can save you from potential issues down the line.
#### Advanced Tips
If you want to take it further, consider customizing some aspects of your linear shafts based on unique requirements—like adjusting tolerances for high-speed applications or integrating smart sensors for real-time monitoring!
Should you have any lingering questions about compatibility or advanced materials, don’t hesitate to reach out to suppliers who specialize in motion systems; their expertise could reveal solutions tailored just for you!
By following these practical steps, you'll not only choose an effective linear shaft but also lay down a strong foundation for enhanced performance in all future projects!
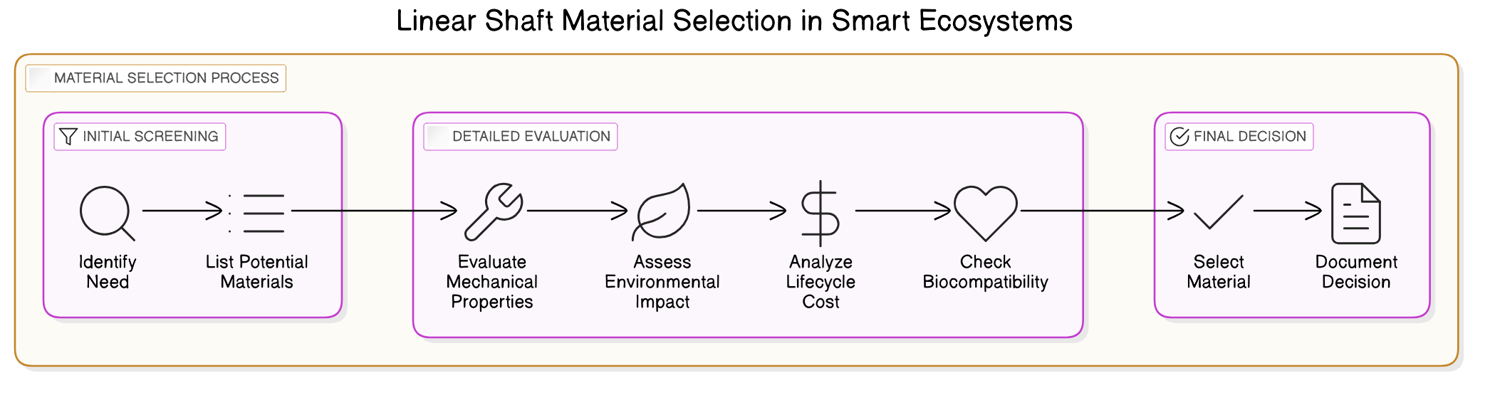
The Future of Linear Shafts: Innovations and Emerging Applications?
Conclusion: Optimizing Motion Systems with High-Quality Linear Shafts
Moreover, the integration of bearings must align with specific operational requirements—choosing ball bearings for high-speed applications or plain bearings for lower speeds with greater load capacities can significantly impact system performance. Additionally, implementing effective lubrication strategies not only reduces wear but also ensures smooth functionality across varying environments.
As we look to the future of motion systems, it's clear that this trend toward increased efficiency and precision will continue to evolve. Now is the time to take action—assess your current systems and explore how these insights can enhance your operations. By thoughtfully selecting materials, refining design specifications, and adhering to robust maintenance protocols, you can achieve remarkable improvements in performance and longevity. How will you adapt to stay ahead in this rapidly advancing landscape?
Reference Source
Linear Motion Technology | Bosch Rexroth Singapore
Components, systems and mechatronic solutions from Bosch Rexroth enable reliable guiding, precise positioning, and advanced handling.
Source: Bosch RexrothLinear Motion Systems Ltd: Home Page
Welcome to Linear Motion Systems, we are the UK leader's in the supply of bespoke engineered bearing & driven rotary solutions. With a collective knowledge ...
Source: Linear Motion Systems LtdLinear Motion Systems
Linear motion products by CMCO are specially designed for a variety of industrial and commercial applications and used for precise motion control.
Source: Columbus McKinnonLinear Motion Systems
The diverse range of Thomson guide and drive systems can be configured to work in harsh environments, at high speeds and in high-precision applications.
Source: Thomson LinearLinear Motion Technology
Components, systems and mechatronic solutions from Bosch Rexroth enable reliable guiding, precise positioning, and advanced handling. In many industries, such ...
Source: Bosch RexrothLINEAR MOTION SYSTEMS
Page 1. LINEAR MOTION SYSTEMS. Simplicity® Self-lubricated Bearings, Guides, Systems & Slides. 800.962.8979 www.pacific-bearing.com SMOOTH & QUIET LINEAR MOTION ...
Source: Моушн-ПродактсLinear Plain Bearing Systems, Actuators, Shafts and Guides
PBC Linear Europe provides maintenance-free, self-lubricating linear plain bearing systems, actuators, linear roller guides, ...
Source: PBC Linear EuropeLinACE™ InAxis Linear Absolute Magnetic Shaft Encoder
LinACE™ is an extremely robust absolute linear cylindrical encoder system designed for integration into hydraulic, pneumatic and ...
Source: RLS encoder
Related Discussions