Summary
This article delves into the fascinating world of sleeve bearings, highlighting innovative advancements that can significantly influence your choices. It offers valuable insights for anyone looking to optimize their bearing selection based on modern technologies and sustainability practices. Key Points:
- Explore advanced materials like metal matrix composites and nano-structured coatings that enhance sleeve bearing performance in extreme conditions.
- Discover how digital twin technology and AI-driven diagnostics are transforming predictive maintenance, leading to reduced downtime and increased efficiency.
- Learn about the importance of sustainable lubricants and eco-friendly designs in minimizing environmental impact while extending product lifecycles.
What Makes Sleeve Bearings Tick? Unpacking the Fundamentals
My First Sleeve Bearing Experience: A Tale of Trial and Error
“Did you even check if it was aligned properly?” Mark's voice echoed in my head, mixing with the clamor of metal grinding against metal. Honestly? No, I hadn’t—who knew alignment could make or break everything?
Frustration bubbled up inside me; I'd miscalculated the load capacity too. It wasn’t just about size; there were specs and measurements staring back at me from this new reality—a harsh lesson learned. The clock read 3 PM, but it felt like an eternity wasted on guesswork—my notebook now filled with scribbles of what went wrong instead of solutions.
At that moment, all my initial excitement faded into disbelief—I didn’t expect it to be this hard.
Comparison Factor | Material Type | Load Capacity | Speed Rating | Temperature Range | Lubrication Method |
---|---|---|---|---|---|
Bronze Sleeve Bearings | Bronze Alloy | High load capacity suitable for heavy machinery | Moderate speed rating, typically up to 3000 RPM | -40°C to 200°C, depending on alloy composition | Oil or grease lubrication is commonly used |
Plastic Sleeve Bearings | Polymer Composites | Lower load capacity, best for lightweight applications | Higher speed ratings possible, often exceeding 5000 RPM | -50°C to 120°C, limited thermal stability under high loads | Self-lubricating properties reduce maintenance needs |
Stainless Steel Sleeve Bearings | Stainless Steel Alloys | Excellent corrosion resistance with moderate load bearing capabilities | Lower speed ratings compared to bronze but can handle intermittent higher speeds | -20°C to 150°C, good for wet environments | Requires external lubrication due to lack of self-lubricating properties |
Ceramic Sleeve Bearings | Ceramic Materials | Very high load capacities and superior wear resistance | Can achieve very high speeds (upwards of 10000 RPM) | -200°C to 1200°C; excellent heat tolerance | Often requires specialized lubricants or dry running conditions |
The Turning Point: Overcoming Initial Sleeve Bearing Challenges
I couldn’t shake off the feeling of being watched as people began to shift uncomfortably. Some were flipping through manuals on nearby tables, while others stared blankly at product labels like they were reading hieroglyphics. “This one?” I asked hesitantly, pointing to a bearing with a 250N load capacity.
Mark shook his head slowly, “Maybe... but are you sure it’ll fit your motor?” The uncertainty lingered in the air like fog; we all sensed it was crucial to nail this down before anyone else lost patience.
Then came a soft voice from behind us—an older gentleman offered, “Have you considered looking into alignment tolerances? That can make or break your project.” His suggestion hung there for a moment before we exchanged knowing glances; perhaps we weren’t alone in our struggles after all.
How We Help You Choose the Right Sleeve Bearing Solution
Across the aisle, another customer chimed in, “Have you checked the alignment specs? It could be crucial.” The tension was palpable; some team members nodded while others exchanged skeptical glances. “What if this doesn’t work?” one worried voice piped up, highlighting our collective uncertainty.
Despite trying to follow advice and recalibrating our choices based on newfound insights, doubt loomed large. We debated next steps but remained stuck at a crossroads—no clear path forward emerged as we weighed risks against potential rewards. But nobody could say whether this attempt would finally lead us in the right direction.
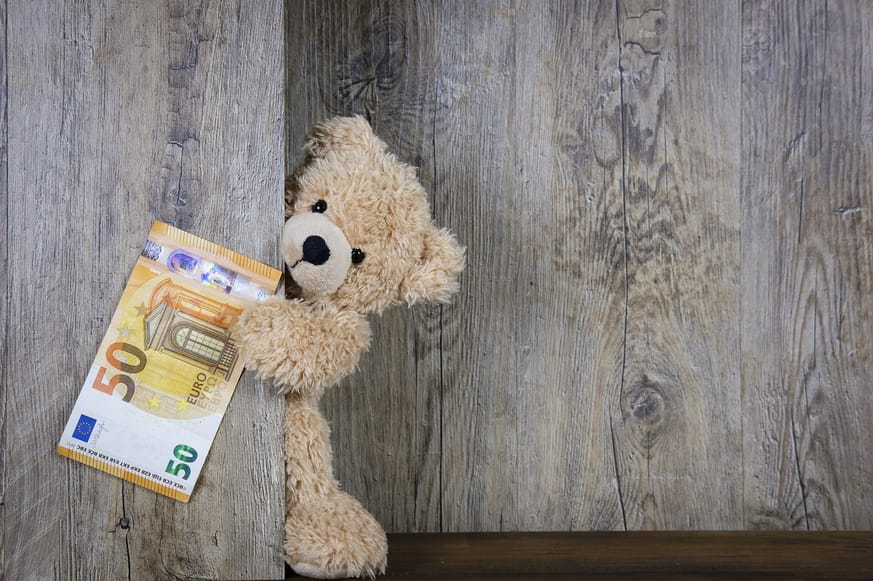
Common Sleeve Bearing Questions: A Quick FAQ
Another question that often arises is: **Do sleeve bearings require lubrication?** Absolutely! While some are self-lubricating (like those made from sintered bronze), others will need regular maintenance to keep them running smoothly. I’ve seen firsthand how neglecting lubrication can lead to premature wear and tear, so don’t skip this step!
Lastly, many people wonder about the impact of shaft alignment on performance. It’s crucial! Misalignment can cause uneven wear and shorten the lifespan of your bearing significantly. Ensuring everything is properly aligned may take a bit more effort upfront but pays off in efficiency and longevity down the line.
So next time you're considering sleeve bearings for your project, remember these key points—they could save you a lot of hassle later on!
Beyond Basics: Exploring Different Sleeve Bearing Materials and Designs?
The Sleeve Bearing Dilemma: Friction vs. Durability – Finding the Balance
Hands-On Guide: Selecting and Installing Your Sleeve Bearing
When it comes to ensuring the smooth operation of machinery, selecting the right sleeve bearing is crucial. Sleeve bearings play a vital role in reducing friction between moving parts, thus enhancing efficiency and longevity. Based on my experience and what many often overlook, properly choosing and installing these components can save you time, money, and headaches down the line.
I remember when I first began working with machinery; I faced challenges due to improper bearing selection. Many people don’t realize that factors such as material choice, lubrication type, and alignment can make or break your project’s success. So let’s dive into some straightforward steps to help you select and install your sleeve bearing effectively.
#### Step-by-Step Installation Guide
1. **Identify Your Requirements**
Determine the application specifics: load capacity, speed requirements, and environmental conditions (e.g., exposure to moisture or chemicals). This will guide your choice of bearing material—be it bronze for wear resistance or plastic for lightweight applications.
2. **Select the Right Material**
Choose a material that suits your needs:
- **Bronze:** Great for high-load applications requiring durability.
- **Plastic:** Lightweight with good corrosion resistance.
- **Composite Polymers:** Offer excellent performance in diverse conditions.
3. **Match Inner Diameter to Shaft Size**
It's essential that the inner diameter of the sleeve bearing matches your shaft size precisely (no more than ±0.01 mm tolerance). This prevents wobbling or misalignment during operation—trust me; you don’t want unexpected vibrations!
4. **Choose Lubrication Wisely**
Decide whether oil or grease is best suited for your application:
- For high-speed operations: Oil is preferable as it provides better cooling.
- For lower speeds with less frequent maintenance: Grease works well but may require periodic replenishment.
5. **Prepare for Installation**
Gather necessary tools like a caliper for measurements, lubricant applicator (either grease gun or oil can), and perhaps an alignment tool if precision is critical in your setup.
6. **Ensure Proper Alignment**
Now we’re getting to a key step! Align the sleeve bearing carefully on its mount—this ensures that everything runs smoothly without extra wear from misalignment.
7. **Create Adequate Clearance**
Allow sufficient clearance within housing structures to accommodate thermal expansion during operation (usually 0.1-0.2 mm depending on materials used).
8. **Install with Care**
Gently slide the bearing onto its housing without forcing it—this avoids damaging both components! If using grease, apply a thin layer inside before installation; it'll help reduce initial wear during startup.
9. **Test Before Full Operation**
After installation, manually rotate the shaft to ensure there’s no binding or abnormal noise—a quick check saves future trouble!
#### Advanced Tips & Reminders
If you're looking for even smoother operations down the road, consider regularly checking lubrication levels according to usage frequency—it helps maintain optimal performance over time! Also, if you find yourself frequently replacing bearings due to wear-and-tear issues in high-speed applications, investing in higher-quality materials might be worthwhile.
For those adventurous enough looking into advanced modifications—if you want further optimization—you could explore adding temperature sensors near bearings; they provide real-time data which can prevent overheating before it becomes problematic.
Remember: selecting and installing sleeve bearings isn’t just about following steps—it’s about understanding how each component interacts within your system! Happy building!
Future of Sleeve Bearings: What Innovations Lie Ahead?
Choosing the Right Sleeve Bearing: A Summary and Next Steps
Next on your checklist should be the lubrication method. If you're looking for self-lubricating solutions, oil-impregnated bearings are a solid choice. Alternatively, for setups requiring external lubrication, consider those equipped with grease fittings for easier maintenance.
Operating conditions also merit careful consideration—think about temperature ranges and any environmental elements such as moisture or corrosive substances that could jeopardize material integrity. Lastly, ensure you assess compatibility with shaft dimensions by taking clearance and fit tolerance into account; this will optimize overall performance.
As trends in technology advance and applications evolve, it’s crucial to stay informed and adaptable in your choices. Now is the time to take action: analyze your specific requirements thoroughly and choose a sleeve bearing that aligns seamlessly with them! Your next step could lead you toward enhanced operational efficiency—are you ready to make that leap?
Reference Source
SLEEVE BEARING GUIDE
To select the right Thomson™ Nyliner™ bearing for your application, several important design factors must be considered. These are bearing load, shaft speed, ...
Source: Specialty Product TechnologiesBearing Sleeve Types: Uses, Materials and Selection Guide
When choosing bearing sleeve types, you should consider whether you need an opening, how big it should be, and how tall you are, rather than clearance and ...
Source: iskbearing.comThe Ultimate Guide To Sleeve Bearings And Bushings
In this article, we'll take an in-depth look at the characteristics and applications of sleeve bearings, bushings, and bearings, clarifying their functions, ...
Source: aubearingWhat is a Sleeve Bearings: The Ultimate Guide | ISK BEARINGS
If you are not sure which bushing bearing to pick, we suggest talking to professional engineers or ISK BEARINGS. This will help your equipment perform better ...
Source: iskbearing.comUnderstanding Bearing Types: Your Guide to Making the ...
Discover the different types of bearings and learn how to select the right one for your application to enhance machinery performance and longevity.
Source: Bearing & Drive SystemsBearings 101: Types, Failures, & Strategic Selection
Explore our guide on bearing types, failure causes, self-lubricating plastic bearings, and material comparisons to aid in strategic bearing selection.
Source: TriStar PlasticsA Guide to Choosing the Right Bearing for Your Application ...
Size and Fit: Ensure the bearing fits perfectly within your machinery. A proper fit prevents unnecessary stress and premature wear. Lubrication: ...
Source: znlbearings.comThe Ultimate Guide to Sleeve Bearings and Bushings - Huading
The performance advantages of sleeve bearings include lower cost, less maintenance, reduced noise at low speeds, and easier installation where ...
Related Discussions