Summary
Choosing the right ball nut for your machinery can significantly impact performance and longevity. In this guide, we explore the latest advancements that can help you make an informed decision and optimize your machinery`s efficiency. Key Points:
- Explore advanced materials like ceramic-reinforced composites for better wear resistance and lifespan.
- Learn how AI-driven sensors in ball nuts enable predictive maintenance, reducing downtime effectively.
- Discover the benefits of hybrid designs that combine materials for enhanced performance and cost-effectiveness.
What Makes the Right Ball Nut Crucial for Your Machinery`s Performance?
A Manufacturer`s Tale: The Struggle to Find the Perfect Ball Nut
The misalignment caused a 20% spike in production time, pushing deadlines further away. "We spent two weeks trying to fix it," Mark admitted. "At one point, I was staring at the machine, thinking, 'What are we missing here?'" The team even reached out to the supplier, but the response was slow. "They kept saying, 'We’ll look into it,' but nothing changed," Mark added. "It was frustrating—like hitting a wall over and over."
The emotional toll was evident. "You start doubting everything," Mark shared. "Was it the supplier? Did we miss something in the specs? It was a mess." Eventually, they decided to involve the manufacturer directly. "We didn’t have a choice," Mark said. "But even then, I wasn’t sure if it’d work. When things go sideways, you just have to roll with it."
Key Factors | Description | Importance | Considerations |
---|---|---|---|
Material Selection | Choose between steel, brass, or plastic based on load capacity and application. | Critical for durability and performance. | Corrosion resistance in harsh environments. |
Preload Configuration | Adjust preload to minimize backlash while enhancing rigidity. | Affects operational precision and wear rate. | Balance between stiffness and wear considerations. |
Recirculation System Type | Decide on endcap or deflector systems based on speed requirements. | Influences performance and maintenance needs. | Compatibility with existing machinery design. |
Installation Precision | Ensure proper alignment during installation to prevent accelerated wear. | Essential for long-term functionality of machinery. | Use compatible lubricants tailored to the system. |
Advanced Technology Integration | Incorporate smart technologies like sensors for real-time monitoring. | Enhances operational efficiency and predictive maintenance capabilities. | Stay updated with technological advancements in ball nut design. |
Turning Point: How One Company Solved Their Ball Nut Dilemma
Mark’s voice grew sharper. "We’re not just wasting time—we’re losing clients. Two orders have already been pushed back. If this keeps up, we’re looking at a 15% hit to our quarterly revenue."
The team decided to cut ties with the supplier and take matters into their own hands. "We’re testing every ball nut ourselves," Mark declared. "No more relying on promises." It was a gamble, but one they couldn’t afford not to take. And then, silence—no one knew if it would work, but they all knew they had to try.
How We Helped Identify the Ideal Ball Nut for Their Needs
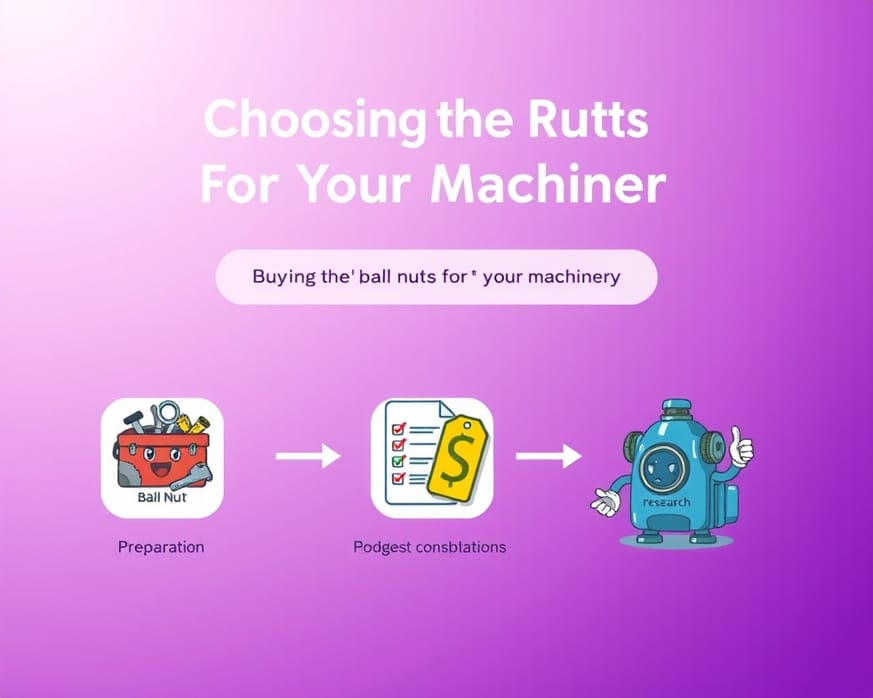
Ball Nut FAQs: Answering Your Most Common Questions
Ball nuts are pretty ingenious little components that operate on the principle of recirculating balls. This setup significantly reduces friction between the screw and nut assembly, which means smoother motion and higher efficiency for your machinery. Quite fascinating, isn't it? 💡
Now, many people often overlook the materials used in ball nuts. The most prevalent option is steel, known for its strength and durability—perfect for heavy-duty applications. However, there are also brass and plastic variations that might be lighter but could have some limitations in terms of load capacity. It’s essential to consider what best fits your specific needs!
You might also wonder about customization options like size or preload levels. Preload is particularly interesting as it adjusts the clearance between those tiny ball bearings and their raceways. A well-set preload can enhance rigidity while minimizing any potential backlash during operation.
In my experience, balancing these factors can feel overwhelming at first, but it's all about understanding your application’s requirements. After all, choosing the right ball nut not only ensures optimal performance but also contributes to greater longevity in your machinery.
So next time you're diving into this selection process or pondering over any specifics—remember you’re not alone! Many folks find themselves navigating through similar choices too! 😊
Is There a One-Size-Fits-All Ball Nut Solution?
The Debate: Balancing Cost and Quality in Ball Nut Selection
Step-by-Step Guide to Choosing and Installing the Right Ball Nut
Choosing the right ball nut for your machinery is crucial, not only for optimal performance but also for ensuring longevity and efficiency. I recommend following these steps because I've seen firsthand how a well-chosen ball nut can make all the difference in machine operation, while an improper selection can lead to frustrating downtime and costly repairs.
Many people overlook key factors when selecting a ball nut, which can lead to issues like backlash or premature wear. For instance, in my early days of working with machinery, I encountered a situation where a simple oversight in load capacity led to significant operational challenges. Learning from that experience has made me appreciate the importance of making informed choices.
#### Step-by-Step Process
1. **Understand Your Requirements**
- Before diving into options, assess your machinery's specific needs. Consider factors such as load capacity (how much weight it will bear), precision levels required, and environmental conditions (like exposure to moisture or corrosive elements).
2. **Select the Material**
- Choose between hardened steel for general applications or stainless steel if you need corrosion resistance in harsh environments. Remember that stainless steel tends to be more durable under challenging conditions.
3. **Determine Preload Needs**
- Decide on the preload level necessary for minimizing backlash during operation. A higher preload often results in increased stiffness but may also lead to faster wear—finding the right balance is key!
4. **Choose Your Recirculation System**
- Look at whether you need an endcap or deflector type recirculation system based on your speed requirements and durability preferences. This choice affects both performance and maintenance needs down the line.
5. **Install with Precision**
- Proper alignment during installation cannot be overstated; misalignment may cause accelerated wear over time.
- Use compatible lubrication tailored to both material type and operating conditions (I personally prefer using synthetic lubricants as they tend to last longer).
6. **Torque Evenly**
- When securing mounting screws, apply torque evenly across all screws—this helps prevent distortion which could compromise function.
7. **Customization Options**
- If applicable, consider custom features like special coatings or seals that enhance performance based on specific application demands.
#### Advanced Tips
If you're looking to take your knowledge further or tackle common installation issues, here’s a little insight: always keep an eye on temperature variations during operation; excessive heat can weaken components over time! Additionally, if you find yourself dealing with particularly heavy loads regularly, investing in advanced monitoring tools might provide insights into wear patterns before they become critical problems.
By following these steps diligently—and applying some personal care along the way—you'll not only choose the right ball nut but also set up your machinery for success!
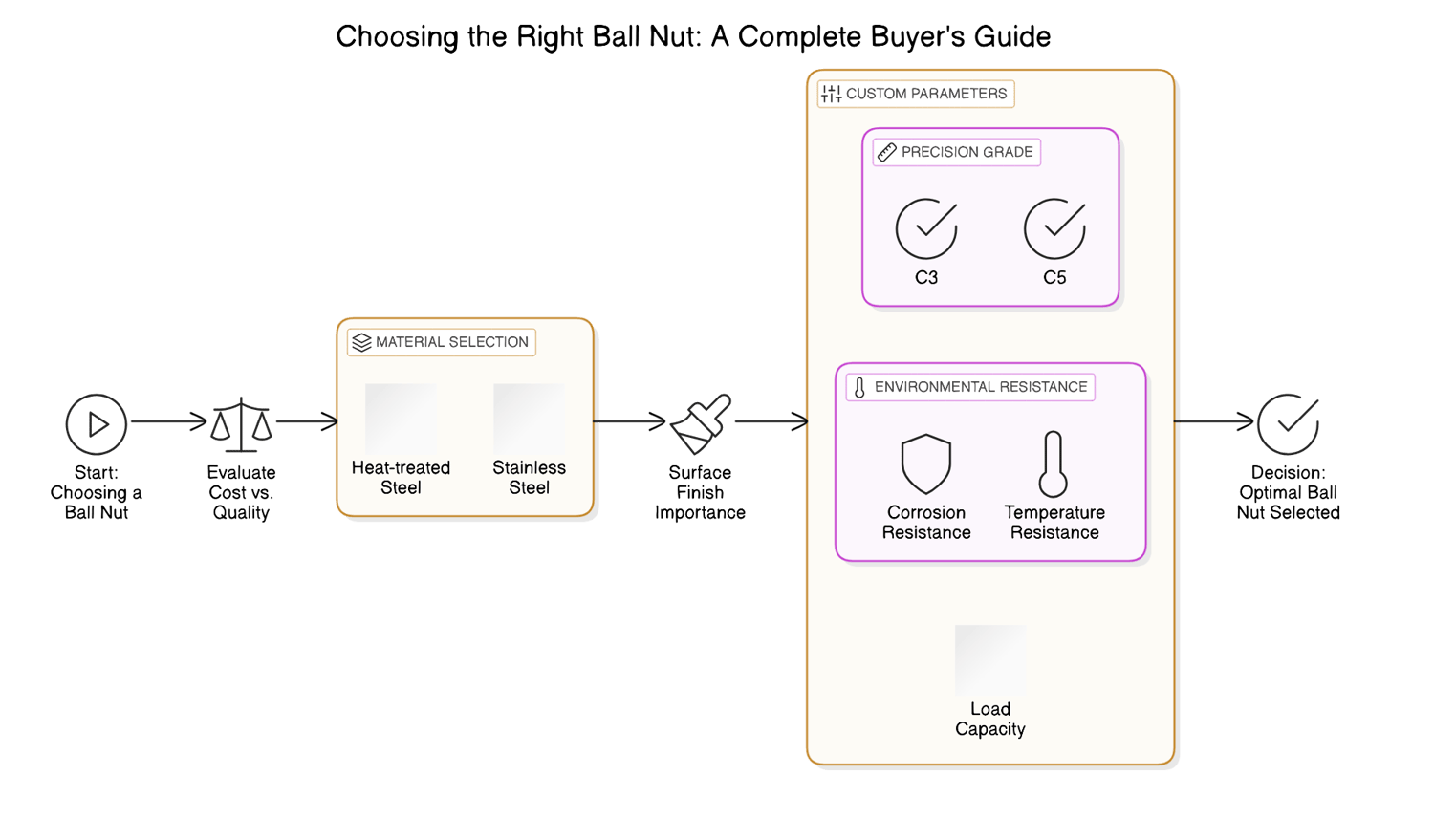
What’s Next for Ball Nut Technology and Innovation?
Conclusion: Making an Informed Decision on Ball Nuts for Your Machinery
Don’t forget about precision class! Higher grades might come with a heftier price tag, but they can also provide improved accuracy that could be essential for certain applications. Meanwhile, evaluating load capacity alongside environmental considerations such as temperature fluctuations and humidity levels will help ensure that the ball nut functions effectively under varying conditions.
Ultimately, understanding these elements allows you to enhance machine efficiency while potentially reducing maintenance costs in the long run. This trend toward more tailored solutions won’t be slowing down anytime soon, so how do we adapt our choices accordingly? It’s all about striking that balance between meeting operational needs and staying within budget constraints.
Now is the time to take action! Dive deeper into these considerations and assess which options resonate best with your machinery requirements. Explore what works for you—this method might just be exactly what you need to elevate your operations!
Reference Source
acme and ball - screws & nuts - design guide
which nut configuration best suits your attachment needs – with or without a flange. 3. Once the initial selection has been made, the user should verify his.
Source: Duff Norton AustraliaBallscrew Basics
Very quickly, ground ballscrews are normally fitted with a zero-backlash nut. To do this, the manufacturer loads the nut with oversized balls; or, the ballnut ...
Source: CNCzone.comlead screws vs ball screws
The balls move in the grooves of the shaft and nut whenever the screw rotates, thus minimizing the friction, and allowing effortless linear motion. Due to the ...
Source: ARMPROThe 6 steps of ball screw selection
When choosing a suitable ball screw and nut you need to pay attention to several factors. The most important factors are presented below.
Source: the Tuli shopComparing Machine Screw Jacks and Ball ...
A ball screw jack also uses a threaded metal lift shaft, but the nut is outfitted with rolling balls that can reduce friction between the screw ...
Ball Bearing Guide | Selection, Failure, & More
Precision Nut Torque Calculator · Tools & Guides. Tools & Resources; Buyer's Guide · Ball Bearing Guide. Tools & Guides; 3 Things That Change a Ball Bearing ...
Source: GMN Bearing USAUnderstanding and choosing the right fasteners
Structural fasteners need the bolt to be stronger, so use a standard bolt with stainless nut, but there are applications where a stainless bolt ...
Source: Reddit · r/AskEngineersChoosing the Right Hydraulic Cylinder for Your Industry
Choosing the Right Hydraulic Cylinder for Your Industry: A Buyer's Guide ... Jam Nut (1); Rate Control (1); Stop Collar (1). Excess Inventory ...
Source: Air & Hydraulic Equipment,Inc.
Related Discussions